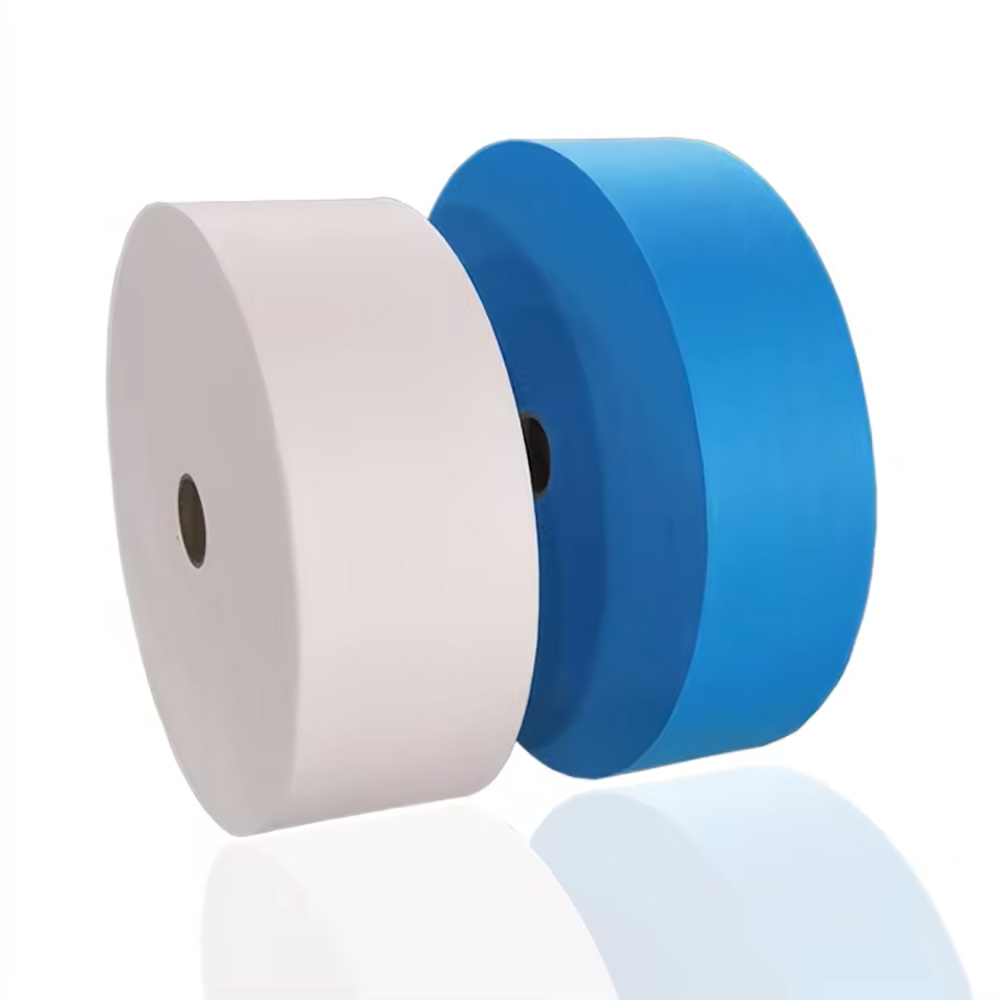
- +8613859957860
- [email protected]
- No.11 Shuangfu Road, Tong’an District, Xiamen, China
Meltblown fabric plays a pivotal role in industries ranging from healthcare to filtration. Its fine fiber structure and unique properties make it an essential material for applications such as face masks, air filters, and insulation. Understanding the science behind meltblown fabric and its various uses is key to appreciating its impact on daily life. This article delves into the production, properties, and diverse applications of meltblown fabric, answering critical questions about its functionality and benefits.
Meltblown fabric is a type of nonwoven material known for its ultra-fine fibers and high filtration efficiency. Unlike woven or knitted textiles, meltblown fabrics are created through a unique process that forms a web of fine polymer fibers without traditional weaving. This results in a lightweight yet strong fabric with excellent barrier properties.
The use of meltblown fabric skyrocketed during the COVID-19 pandemic, as it became a key component in surgical masks and N95 respirators. Its ability to capture particles as small as viruses highlights its exceptional performance as a filtration medium.
Meltblown fabric is manufactured using a process that involves melting thermoplastic polymers, such as polypropylene, and extruding them through fine nozzles. These molten fibers are stretched and cooled to form a fine web. The main steps include:
This process results in a fabric with unique properties, such as high porosity and excellent filtration efficiency.
The primary difference lies in the fiber size and structure:
Both materials are often combined to create SMS (spunbond-meltblown-spunbond) fabrics, leveraging their complementary strengths.
Polypropylene is the polymer of choice for meltblown fabrics due to its:
Polypropylene’s versatility ensures that meltblown fabrics meet the stringent requirements of medical and industrial sectors.
Meltblown fabric is unparalleled as a filter medium because of its:
These features make it indispensable in air and liquid filtration systems.
Meltblown fabric is extensively used in healthcare for products such as:
The fabric’s lightweight and disposable nature make it ideal for single-use medical items.
Meltblown fabric is a cornerstone in filtration technologies. It is used in:
Its ability to combine high efficiency with low pressure drop makes it a preferred choice in these systems.
While both are nonwoven, the differences include:
Understanding these differences helps industries choose the right material for their needs.
The fine, random arrangement of fibers in meltblown fabric ensures:
This unique structure is key to the fabric’s widespread use in demanding environments.
The future of meltblown fabric includes:
These innovations promise to expand the capabilities of meltblown fabrics while addressing sustainability challenges.